CNC technology and the Internet of Things (IoT) – the integration of Industry 4.0
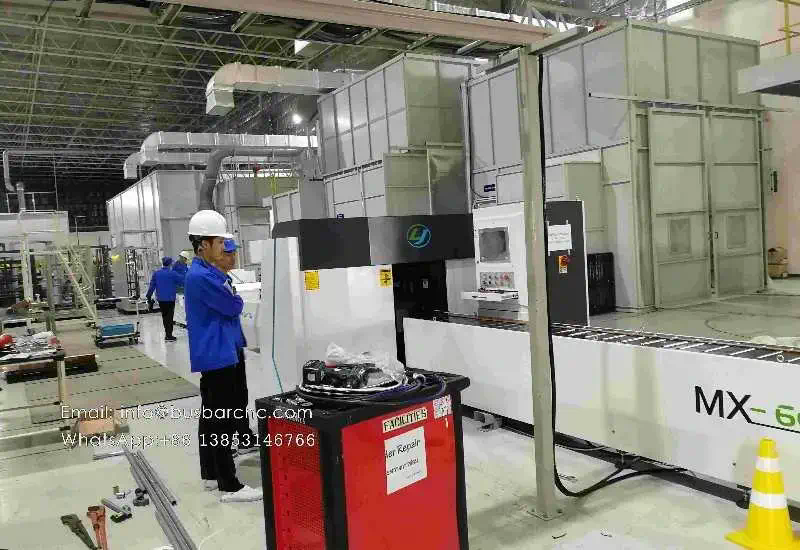
CNC technology and the Internet of Things (IoT) are at the forefront of the integration of Industry 4.0, revolutionizing manufacturing processes and paving the way for greater efficiency, flexibility, and connectivity in industrial operations. In this article, we will delve into the significance of CNC technology and the IoT in the context of Industry 4.0, exploring their impact on the manufacturing landscape and how their integration is shaping the future of industry.
CNC (Computer Numerical Control) technology has been a cornerstone of modern manufacturing for decades, enabling precise and automated control of machine tools and processes. By utilizing computer systems to control machine tools, CNC technology has significantly enhanced the efficiency and accuracy of manufacturing operations, reducing human error and increasing productivity. The integration of CNC technology with the Internet of Things (IoT) has further amplified its capabilities, ushering in a new era of smart manufacturing.
Enhancing Connectivity and Data Exchange with IoT Integration
The Internet of Things (IoT) refers to the network of interconnected devices and sensors that collect and exchange data over the internet. By integrating CNC machines with IoT technology, manufacturers can establish seamless connectivity between different components of the production process, enabling real-time monitoring and control of operations. This connectivity facilitates the exchange of valuable data, allowing manufacturers to optimize processes, predict maintenance needs, and improve overall efficiency.
Improving Predictive Maintenance and Monitoring
One of the key benefits of integrating CNC technology with the IoT is the ability to implement predictive maintenance strategies. By equipping CNC machines with sensors that monitor performance metrics in real-time, manufacturers can detect potential issues before they escalate into costly breakdowns. This proactive approach to maintenance helps minimize unplanned downtime, prolong machine lifespan, and optimize production schedules.
Enhancing Flexibility and Customization in Manufacturing
The integration of CNC technology and the IoT also enables greater flexibility and customization in manufacturing processes. By leveraging real-time data and insights gathered from IoT-connected machines, manufacturers can adapt production processes on the fly, respond to changing demand patterns, and customize products to meet specific requirements. This agility is crucial in today’s fast-paced market environment, where responsiveness and customization are key competitive advantages.
Facilitating Remote Monitoring and Control
Another significant advantage of integrating CNC technology with the IoT is the ability to remotely monitor and control manufacturing operations. Through IoT-enabled dashboards and mobile applications, manufacturers can oversee production processes from anywhere in the world, enabling greater visibility and control over operations. This remote access empowers decision-makers to make informed choices in real-time, optimize workflows, and address issues promptly, enhancing overall operational efficiency.
Driving Efficiency and Cost Savings
The integration of CNC technology and the IoT is driving significant improvements in efficiency and cost savings for manufacturers. By automating processes, optimizing workflows, and streamlining operations through IoT connectivity, manufacturers can reduce waste, minimize energy consumption, and enhance resource utilization. These efficiency gains translate into tangible cost savings and improved profitability, enabling manufacturers to stay competitive in an increasingly dynamic market landscape.
Enhancing Quality Control and Traceability
Quality control is a critical aspect of manufacturing, and the integration of CNC technology with the IoT is revolutionizing how manufacturers ensure product quality and traceability. By capturing detailed data throughout the production process, including machine performance metrics, environmental conditions, and material specifications, manufacturers can track and trace each product from inception to delivery. This level of transparency and traceability not only enhances quality control but also enables manufacturers to meet regulatory requirements and customer expectations.
Leveraging Big Data and Analytics for Insights
The integration of CNC technology with the IoT generates vast amounts of data that can provide valuable insights into manufacturing processes. By leveraging big data analytics tools, manufacturers can analyze this data to identify trends, patterns, and anomalies, enabling data-driven decision-making and continuous improvement. These insights help manufacturers optimize processes, identify opportunities for innovation, and drive operational excellence across the organization.
Overcoming Challenges and Security Concerns
While the integration of CNC technology and the IoT offers numerous benefits, it also presents challenges and security concerns that must be addressed. Cybersecurity threats, data privacy issues, and interoperability challenges are some of the key obstacles that manufacturers may face when implementing IoT-enabled CNC systems. To mitigate these risks, manufacturers must invest in robust cybersecurity measures, implement data encryption protocols, and ensure compliance with relevant regulations to safeguard sensitive information and maintain the integrity of their operations.
Future Outlook: Industry 4.0 and Beyond
As CNC technology and the IoT continue to evolve and converge within the framework of Industry 4.0, the future of manufacturing holds immense promise and potential. The integration of digital technologies, automation, and connectivity is reshaping traditional manufacturing paradigms, enabling new possibilities for innovation, efficiency, and competitiveness. By embracing the transformative power of CNC technology and the IoT, manufacturers can propel their operations into the future and unlock new opportunities for growth and success in the digital age.
In conclusion, the integration of CNC technology and the Internet of Things (IoT) within the context of Industry 4.0 represents a significant milestone in the evolution of manufacturing. By harnessing the combined power of precision machining, automation, connectivity, and data analytics, manufacturers can drive operational excellence, enhance competitiveness, and unlock new avenues for growth and innovation. As Industry 4.0 continues to shape the future of industry, embracing the possibilities offered by CNC technology and the IoT is key to staying ahead in a rapidly evolving and interconnected manufacturing landscape.
https://oaicon.com/