Health and Safety Guidelines for CNC Machining Environments
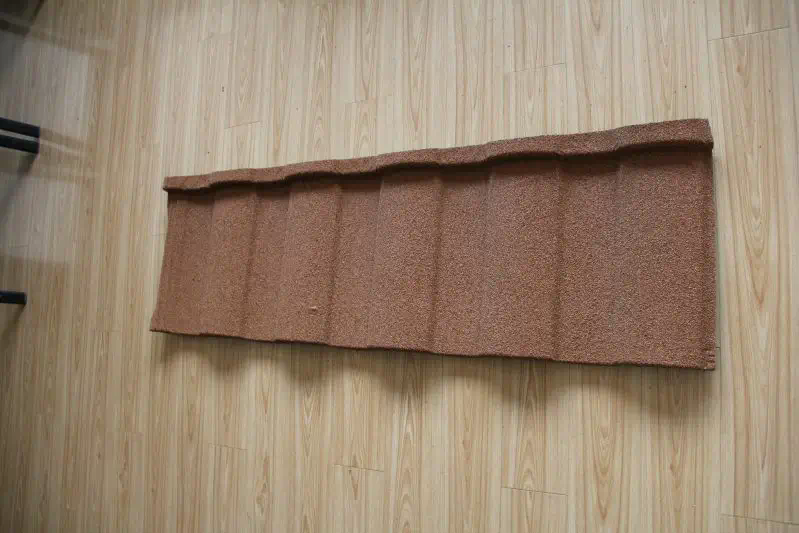
Health and Safety Guidelines for CNC Machining Environments
In the fast-paced world of advanced manufacturing, CNC (Computer Numerical Control) machining plays a critical role in producing precision components for various industries. While CNC machines offer remarkable efficiency and accuracy, they also present potential health and safety hazards to operators and other personnel working in the machining environment. It is essential for companies and individuals involved in CNC machining to adhere to strict health and safety guidelines to ensure a safe working environment. This article will explore the key health and safety considerations for CNC machining environments, along with best practices to mitigate potential risks.
CNC Machining Environment Overview
CNC machining environments typically consist of various equipment, including lathes, mills, routers, grinders, and other specialized machines. These machines are used to cut, shape, and finish raw materials such as metal, plastic, and wood to create precise components according to design specifications. The environment also includes cutting tools, workholding devices, coolant hydraulic pipe bending machine systems, and other accessories necessary for the machining process.
Hazards in CNC Machining Environments
Several hazards are prevalent in CNC machining environments, posing risks to personnel and equipment. These hazards include but are not limited to:
1. Mechanical Hazards: Moving machine parts, sharp cutting tools, and rotating spindles pose the risk of cuts, crush injuries, and entanglement.
2. Chemical Hazards: Coolants, lubricants, and metalworking fluids used in CNC machining can emit harmful fumes and cause skin irritation or respiratory issues if not properly managed.
3. Ergonomic Hazards: Prolonged periods of standing, repetitive motions, and awkward body positions can lead to musculoskeletal disorders among machine operators.
4. Noise and Vibration Hazards: CNC machines generate high levels of noise and vibration, which can contribute to hearing loss and other health issues if adequate measures are not in place.
5. Electrical Hazards: CNC machines are powered by electricity, presenting the risk of electrical shocks and fires if electrical systems are not maintained properly.
Health and Safety Guidelines
To mitigate the aforementioned hazards and ensure a safe CNC machining environment, it is crucial to implement comprehensive health and safety guidelines. These guidelines should encompass various aspects of machine operation, maintenance, and personal protective measures. Here are the key components of effective health and safety guidelines for CNC machining environments:
Personal Protective Equipment (PPE)
Operators and personnel working in CNC machining environments must wear appropriate PPE to protect themselves from potential hazards. This includes safety glasses, face shields, hearing protection, gloves, steel-toed shoes, and other specialized protective equipment based on the specific tasks being performed. Additionally, respiratory protection may be required when working with certain materials or processes that generate airborne contaminants.
Machine Guarding and Safety Devices
All CNC machines should be equipped with adequate guarding and safety devices to prevent contact with moving parts and cutting tools. This includes perimeter guarding, interlocking safety doors, emergency stop buttons, and presence-sensing devices to ensure that machines cease operation if a person or object enters a hazardous area. Regular inspection and maintenance of these safety features are essential to their effectiveness.
Safe Operating Procedures
Establishing and enforcing safe operating procedures is crucial for minimizing risks in CNC machining environments. This includes proper machine setup, tool selection, workpiece clamping, and verification of program parameters before initiating machining operations. Operators should receive thorough training on these procedures and adhere to established protocols at all times.
Workplace Ergonomics
Addressing ergonomic hazards is vital for promoting the health and well-being of machine operators. Workstations should be designed to minimize physical strain, and ergonomic principles should be applied to the layout of controls, tooling, and material handling systems. Regular breaks, job rotation, and stretching exercises can also help reduce the risk of musculoskeletal disorders associated with repetitive tasks.
Hazardous Material Management
Proper management of hazardous materials, such as metalworking fluids and solvents, is essential for preventing exposure-related health issues. This includes maintaining adequate ventilation systems, providing training on safe handling and storage practices, and conducting regular monitoring for airborne contaminants. Additionally, implementing measures to minimize the use of hazardous materials, such as exploring alternative cutting fluids, can further reduce risks.
Noise and Vibration Control
To address noise and vibration hazards, CNC machining environments should incorporate sound-dampening enclosures, vibration isolation mounts, and acoustic barriers where feasible. Regular noise level measurements should be conducted to ensure compliance with occupational exposure limits, and hearing protection should be provided to personnel working in high-noise areas.
Electrical Safety Measures
Adhering to electrical safety measures is crucial for preventing electrical accidents in CNC machining environments. This includes routine inspection and maintenance of electrical systems, proper grounding of machines, and use of ground fault circuit interrupters (GFCIs) where applicable. Personnel should also be trained to identify and report electrical hazards promptly.
Emergency Response and Evacuation Procedures
In the event of an emergency, such as a fire, chemical spill, or machine malfunction, clear emergency response and evacuation procedures should be in place. This includes providing accessible fire extinguishers, first aid kits, and emergency eyewash stations, as well as conducting regular drills to ensure personnel are prepared to respond effectively in emergency situations.
Training and Awareness Programs
Regular training and awareness programs play a pivotal role in promoting a culture of safety in CNC machining environments. All personnel, including operators, maintenance staff, supervisors, and management, should receive comprehensive training on health and safety practices, as well as ongoing updates on industry best practices and regulatory requirements.
Regulatory Compliance
Staying abreast of relevant health and safety regulations, such as OSHA (Occupational Safety and Health Administration) standards in the United States, is essential for ensuring compliance with legal requirements. Companies should regularly review and update their health and safety policies to align with current regulations and industry standards.
Conclusion
Maintaining a safe and healthy CNC machining environment requires a proactive approach that encompasses risk assessment, hazard mitigation, and continuous improvement of health and safety practices. By prioritizing the implementation of comprehensive health and safety guidelines, companies can safeguard the well-being of their personnel and minimize the risk of workplace accidents and occupational illnesses. Furthermore, fostering a culture of safety awareness and accountability among all individuals involved in CNC machining is integral to sustaining a secure working environment. Through diligent adherence to established guidelines and ongoing commitment to best practices, the industry can continue to harness the full potential of CNC machining while ensuring the welfare of its workforce.
https://oaicon.com/