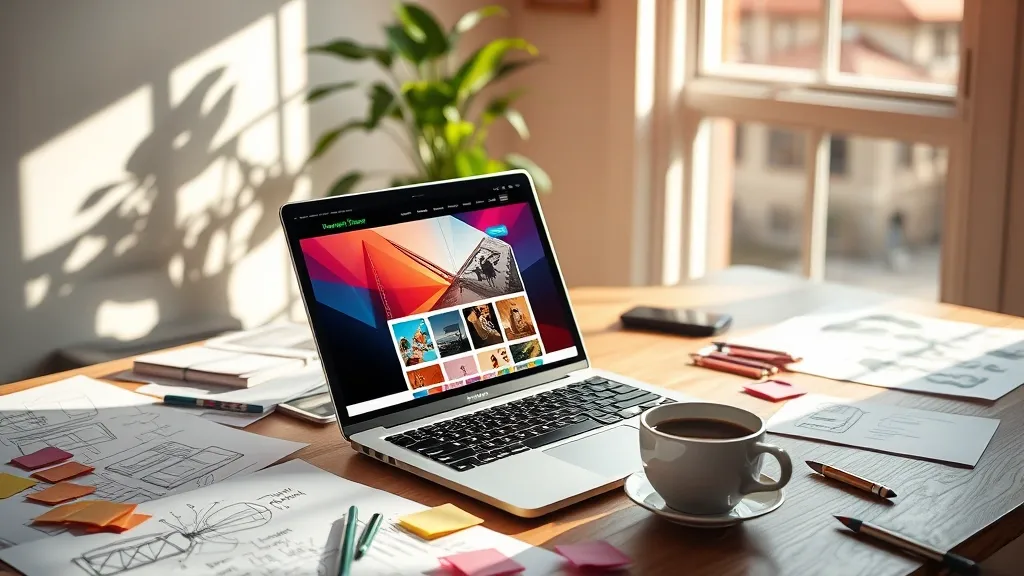
Unlock Your Brand’s Potential with a Custom WordPress Website
Your Website: The Digital Playground for Your BrandOkay, so let’s be real for a sec. Your website is like the ultimate hangout spot for your brand. ...
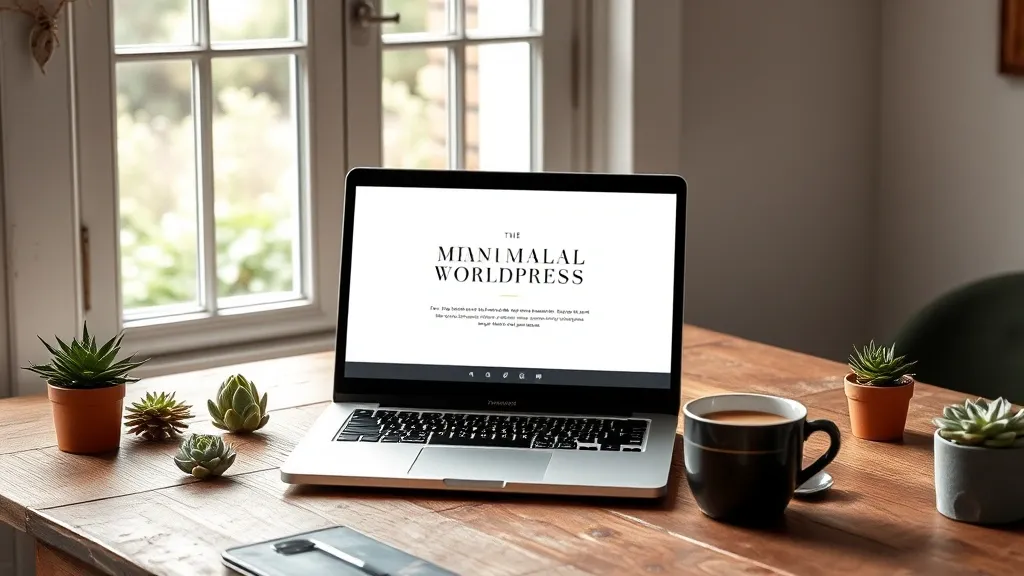
Unlock the Power of Simplicity: Top Simple WordPress Themes for 2025
Simplicity is the New Black: Why Less is More in 2025You ever notice how sometimes less just feels like... well, more? It’s like when you clean out ...
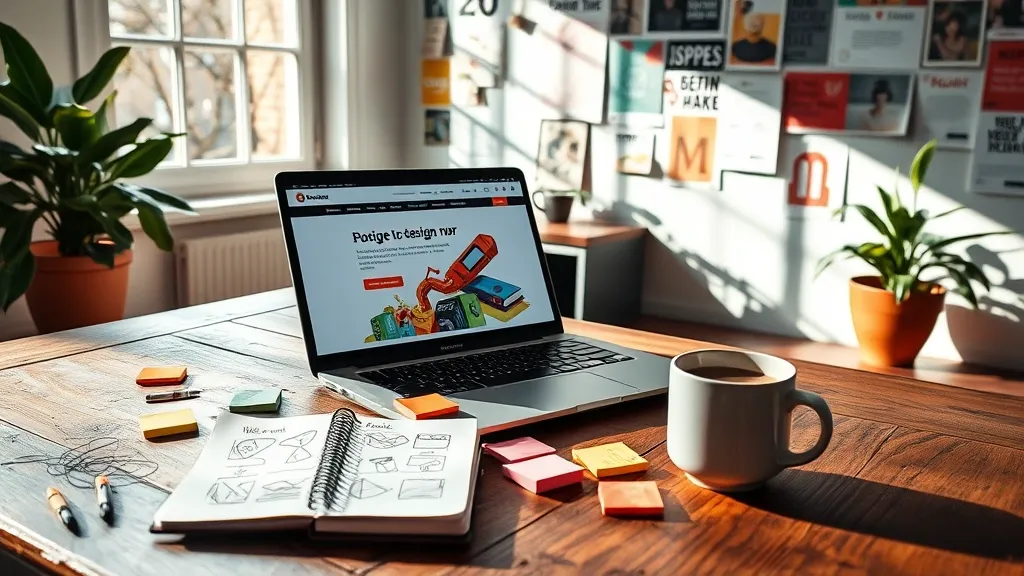
Unlock Your Vision with a Custom WordPress Site: Create Your Unique Online Identity
Why Fit In When You Were Born to Stand Out?You ever hear that saying, Why fit in when you were born to stand out? It’s got a nice ring to it, right?...
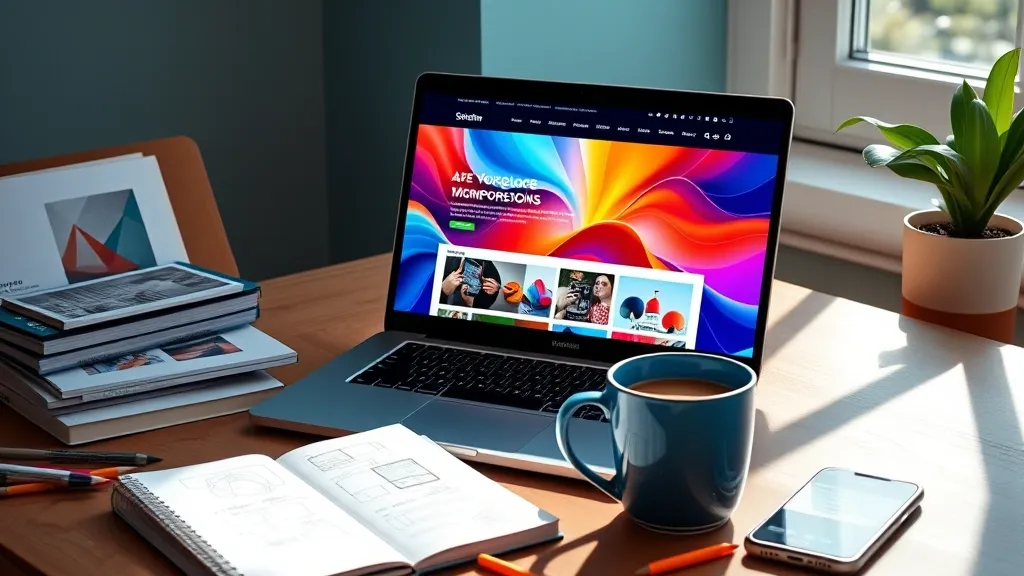
Unlock Stunning WP Templates: Your Guide to Free Downloads in 2025
Diving into the Treasure Trove: Where to Find Hidden GemsOkay, so you’re on the hunt for some killer WordPress templates without breaking the bank? ...
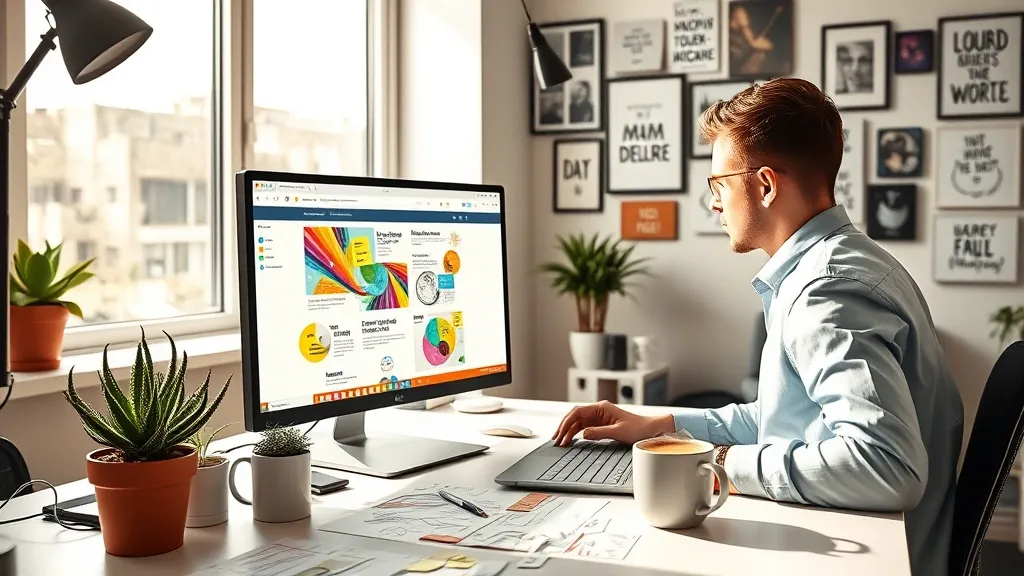
Transform Your Vision: Top-Notch WordPress Website Development Services
Unleashing the Digital Unicorn: What Makes a Website Truly Magical?So, you wanna know what makes a website stand out in this crowded online jungle? It...
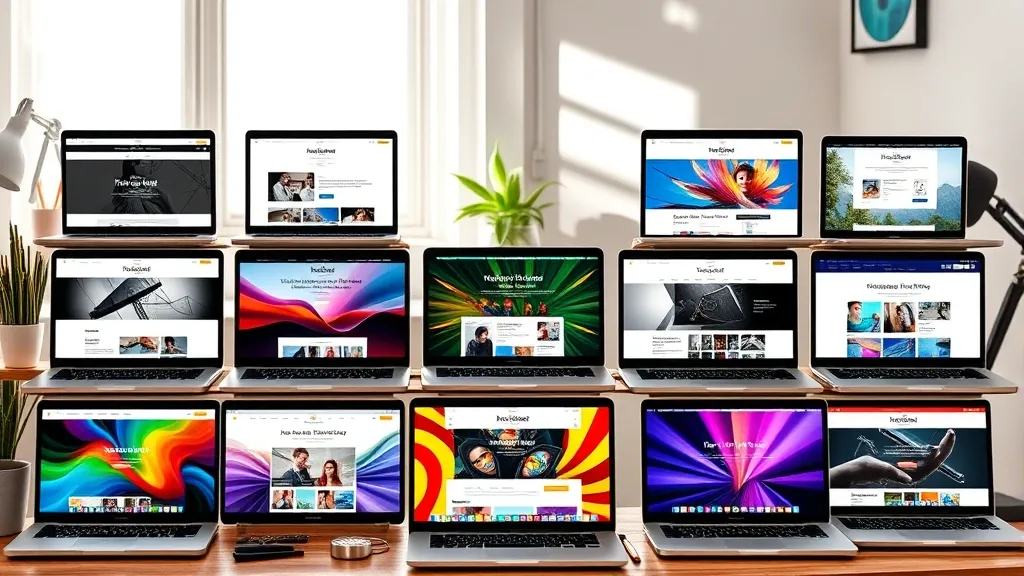
Unlock Your Creativity: Top 10 Free WordPress Themes to Download Today
Doodle Your Dreams: Why WordPress is Your New Best FriendAlright, let’s chat about why WordPress is basically the best buddy you never knew you need...
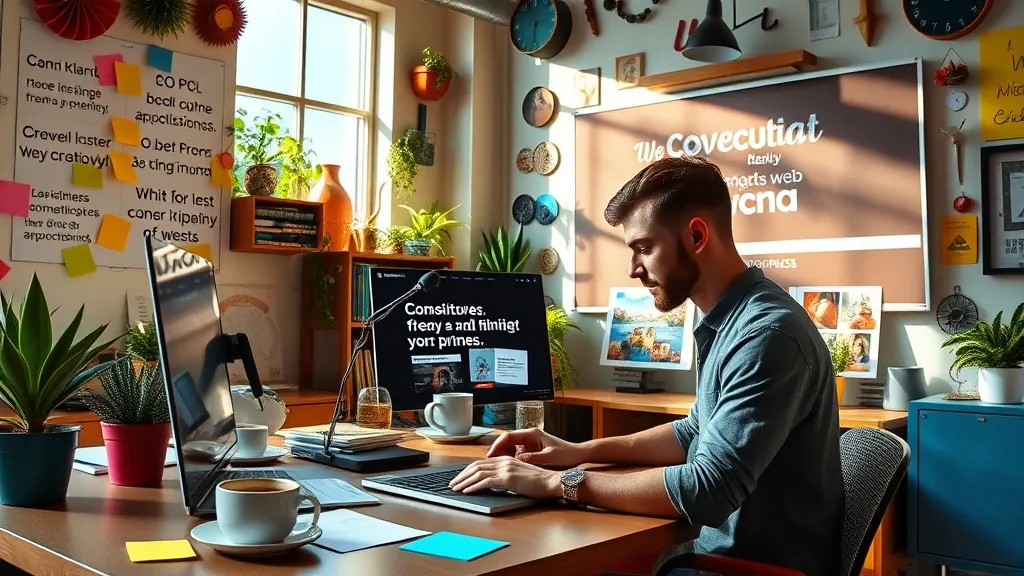
Unlock Your Online Potential with Expert WordPress CMS Development Services
Diving into the Digital Deep End: Why WordPress is Your New Best FriendSo, you're thinking about launching a website? First off, high five! That's a b...
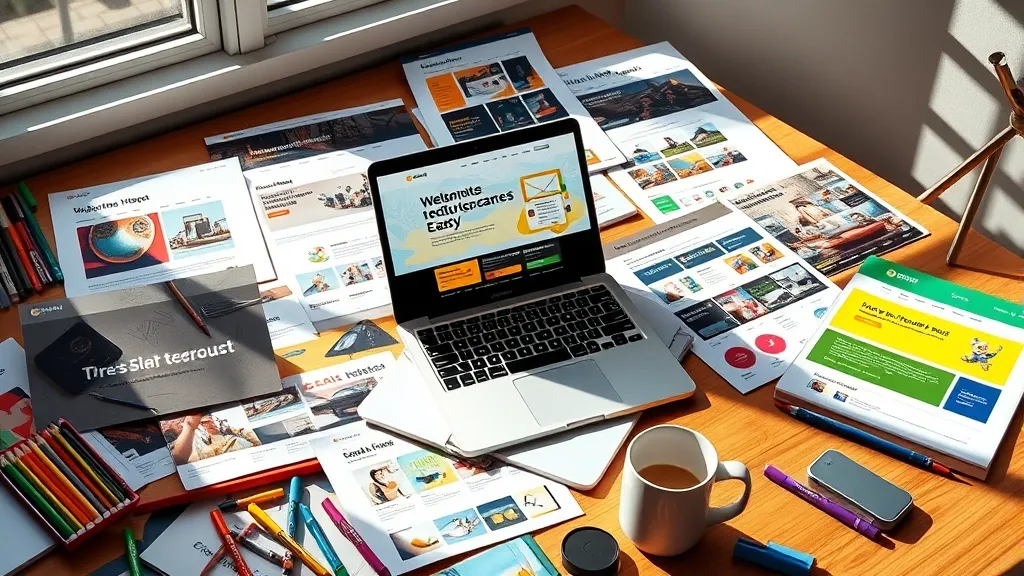
Unlock Your Creativity: 10 Stunning Free WP Website Templates You Can’t Miss
Unleashing the Magic: Why a Template is Your Best FriendOkay, so let’s be real for a second. When you’re staring at a blank screen, trying to figu...
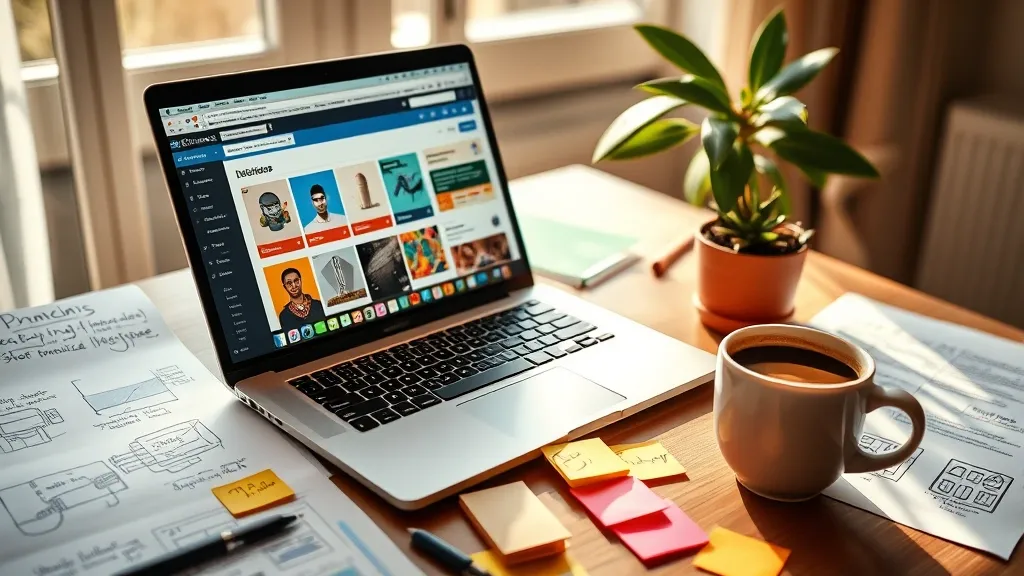
Unlock Your Vision: The Benefits of Custom WordPress Development
Crafting Your Digital Playground: Why Settle for Off-the-Shelf?Alright, let’s dive into it! You know when you go to a store and see a bunch of those...
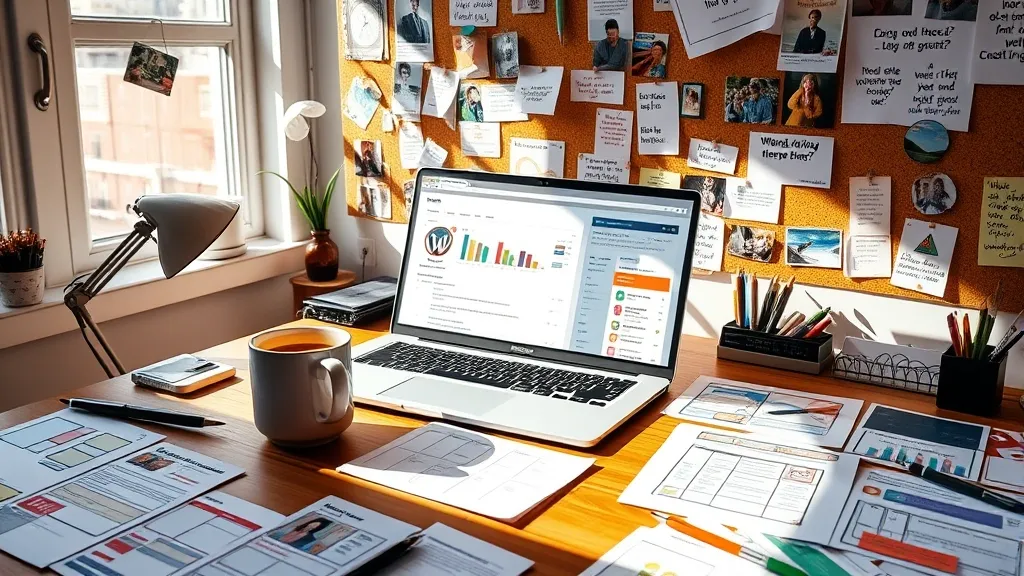
Unlock Your Website’s Potential: Top Free WordPress Themes for Hassle-Free Download
The Treasure Trove of Themes: Where to Dig?Alright, so you’ve decided to give your website a little makeover. Kudos! But now, where do you even star...