Compressive Stress: Definition, Unit, Formula, and Example
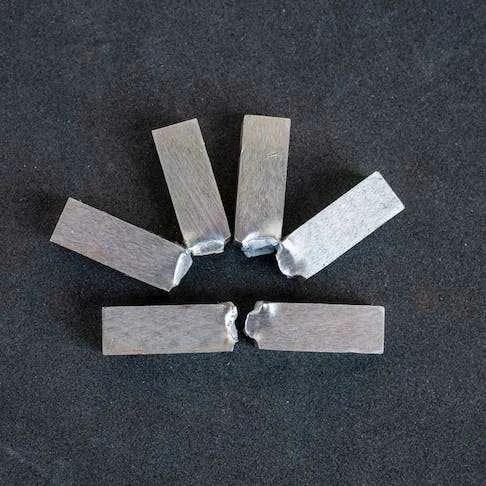
When an outside force is applied in a way that compresses or squeezes an object, it causes a type of stress called compressive stress. Compressive stress forced the atoms in a material to try to move closer together than the crystal structure and interatomic forces allow. The atoms slip past each other on weaker crystal planes and at defects and voids, causing buckling and eventual breakage. Compressive stress is a key principle in engineering and materials science because it influences the strength and durability of structures and materials. Usually, compressive stress is expressed in pascals (Pa) or pounds per square inch (psi). Compressive stress can be calculated by dividing the force applied to an object by the cross-sectional area normal to the force.
Compressive strength is the maximum stress that a material can withstand before breaking under compression. It is a crucial parameter in materials engineering because it determines whether a material is suitable for a given application. This article will discuss compressive stress, how it is calculated, when it occurs, and provide examples.
What Is Compressive Stress?
A compressive stress is a mechanical force where an object is squeezed. A material's molecules move closer to one another as a result of this particular kind of stress, which leads to the object deforming or failing. Understanding the response of materials to compressive stress is a critical part of engineering and materials science because it affects the strength, safety, and longevity of structures and manmade objects both large and small. Robert Hooke—a mathematician and physicist of the 17th century—first proposed Hooke's law. This law describes the relationship between the stress and strain of a material subjected to compressive or tensile forces. Since then, new approaches and methods for calculating and analyzing compressive stresses have been developed in a variety of applications as a result of developments in materials science and engineering.
When Do Compressive Stresses Occur?
Compressive stresses occur when a force is applied to an object, causing it to squeeze. This can happen in several circumstances, such as when something is pressed between two objects or when a material is subjected to a lot of pressure. As structures and materials are frequently subjected to compressive loads, the occurrence of compressive stress within engineered structures is a common event.
What Is the SI Unit of Compressive Stress?
The SI unit for compressive stress is the Pascal (Pa), which is named after the French physicist, Blaise Pascal. One pascal is equal to one newton per square meter (N/m2). Because most materials are so strong, compressive stress is frequently, compressive stress is frequently measured in kilopascals (kPa) or megapascals (MPa) in engineering and materials science. Although atmospheres (atm) and pounds per square inch (psi) are also used to express compressive stress, scientific and engineering applications primarily use the SI unit of pascals.
What Is the Formula of Compressive Stress?
The formula of compressive stress is calculated by force applied to an object divided by its cross-sectional area. In mathematics, it is written as:
Compressive Stress = Force ÷ Area
When force is expressed in newtons (N) and the area is expressed in square meters (m2), the resulting unit of compressive stress is pascals (Pa). Due to the high compressive forces present in many applications, compressive stress is generally expressed in kilopascals (kPa) or megapascals (MPa) in engineering and materials science.
What Is the Dimension Formula of Compressive Stress?
The dimensional formula for compressive stress is given by the following expression:
[M][L]^-1[T]^-2
Dimensional analysis is a mathematical technique used to examine the dimensions or units of measurement of different physical quantities to analyze and comprehend the relationships between them. The physical quantities involved in a problem are expressed in terms of their core dimensions, such as: length, time, mass, and temperature. Dimensional analysis can assist in ensuring the accuracy and consistency of calculations and formulas as well as streamlining unit conversions by keeping track of the dimensions and units of measure of these quantities. Compared to other unit systems, the metric system or the SI units' regular 10-base makes it simpler to convert between different dimensional units.
Compressive stress is defined as the force per unit area acting on a material when it is compressed. The formula is expressed as:
Compressive stress = Force / Area
Where:
- Force is the applied force
- Area is the area of the surface being compressed
The dimensional formula of force can be expressed as:
Force = m×a = kg × ms^-2 = [M][L][T]^-2
The SI unit of mass, kg, is replaced by the dimension of mass, M. The SI unit of length, m, is replaced by the dimension of length, L, and the SI unit of time, s, by the dimension of time, T.
The dimensional formula of area can be expressed as:
Area= m^2=[L]^2
Where:
- L is the dimension of length
Substituting these formulas into the formula for compressive stress, we get:
= Force / Area
= [M][L][T]^-2 / [L]^2
Simplifying this expression, we can divide the dimension of length in the numerator by the square of the dimension of length in the denominator:
[M][L]^1÷[L]^2[T]^-2
= [M][L]^1-2[T]^-2
= [M][L]^-1[T]^-2
What Is High Compressive Stress Mean?
High compressive stress means compressive forces are greater than what a substance or structure can withstand without deforming or failing. The upper limit of high compressive stress depends on the particular material or structure under consideration as well as the usage circumstances. A material or structure may deform, buckle, or fracture when it is subjected to high compressive stresses. In engineering and materials science, high compressive stress is regarded as a serious concern because it can result in structural failure and safety risks in a variety of applications.
What Is an Example of Compressive Stress?
Compressive stresses can be observed in construction applications, where concrete is used to build structures. Concrete is renowned for its compressive strength, with a typical strength of 10,000 psi. An example of compressive stress would be when a load is placed on top of a concrete slab. The application of the external compressive force generates an equal and opposite force within the concrete as the atoms making up the concrete structure attempt to maintain their original interatomic distances.
Steel is typically used to reinforce concrete structures. It increases the material's tensile strength while also increasing the compressive stress. Construction projects can also benefit from rubberized concrete. Rubberized concrete typically has a lower compressive stress than regular concrete. Adding rubber particles to the concrete mixture decreases the material's overall density and has an impact on how the cement particles interlock. Rubberized concrete has the added advantages of increased toughness, durability, and impact resistance while still demonstrating adequate compressive stress for many applications.
Which Material Has a Higher Compressive Stress?
Steel has a higher compressive strength than materials such as aluminum, brass, or copper because of its higher modulus of elasticity. The modulus of elasticity is the measure of a material's ability to resist elastic deformation under stress. A higher modulus means that more stress can be applied before the onset of plastic deformation in compression and subsequent failure. Steel also has a high degree of ductility. This property allows it to bend and deform without cracking even when subjected to powerful compressive forces.
Which Material Has a Lower Compressive Stress?
Compared to other materials, concrete has a low compressive stress. Its compressive strength is about 10,000 psi, which is lower than that of brass, copper, and steel. Concrete's lower compressive strength can be attributed to its composition. It is a composite material made up of sand, gravel, cement, and water. The majority of the material's strength is provided by the sand/gravel aggregate. The cement serves as a binding agent to keep the aggregate particles together. However, due to its porosity, concrete is more prone to breaking or cracking when subjected to compressive forces.
How to Test Compressive Stress?
An overview of how to determine compressive strength is provided below:
- Sample Preparation: Prepare a sample of the substance to be tested. Depending on the test method and the type of material being tested, this may entail cutting, drilling, or molding the material into a particular shape or size.
- Test Setup: Place the sample between two platens on a testing device as part of the test setup. The platens, which are typically made of steel, are intended to evenly distribute the compressive force across the sample's surface.
- Loading: Using a testing apparatus such as a universal testing machine, a compressive load is continuously applied to the sample. The test method typically specifies the rate of loading, which may change depending on the kind of material being tested.
- Measuring Load and Deformation: The testing apparatus measures the amount of force being applied as well as the deformation or displacement of the sample as the compressive load is applied to it. These measurements are used to calculate the material's instantaneous compressive stress and strain.
- Failure and Data Analysis: Increasing load is applied until the sample fails or reaches a predetermined load or deformation limit. The compressive strength of the material is then determined by analyzing the test data.
For more information, see our Compression Test guide.
How to Calculate Compressive Stress?
The formula for calculating compressive stress is expressed below:
Compressive Stress = Force / Area
Where:
- Compressive Stress: The stress that a material experiences as a result of a compressive force.
- Force: Typically expressed in pounds or newtons, is the amount of pressure exerted on the material.
- Area: Typically expressed in square inches or square meters is the cross-sectional area of the material perpendicular to the direction of the force.
To calculate compressive stress using the formula, simply divide the compressive force by the cross-sectional area of the material. It is common to measure the resulting compressive stress in pounds per square inch (psi) or newtons per square meter (N/m2).
What Is the Main Cause of Compressive Stress?
The primary source of compressive stress is the application of an outside force that presses or squeezes a material together, resulting in a reduction in volume. A structure or object pressing down on a material, or the application of a hydraulic or mechanical force are just a few ways this can happen.
What Are the Possible Effects of Compressive Stress?
Compressive stress may have the effect of causing a material to buckle, deform or break. A material experiences compressive stress when a force is applied to it. This stress can cause the material to buckle, crush, or compact. Depending on the material's strength and resilience, compressive stresses could cause permanent deformation or failure of a component or structure.
Is It Possible to Prevent Compressive Stress?
No, compressive stress cannot be completely avoided. When an object is squeezed or pressed, compressive stress results. It is a normal result of many physical processes. Through careful engineering and design decisions, such as the use of materials that are more resilient to compression or the creation of structures that evenly distribute stress, compressive stress may be reduced or managed.
What Is the Difference Between Tensile Stress and Compressive Stress?
Compressive stress happens when a material is squeezed or pressed together, whereas tensile stress happens when a material is pulled apart or stretched. The main distinction between the two is that tensile stress pulls the atoms of the material apart, whereas compressive stress pushes the material together. In engineering and construction, where materials need to be chosen and designed based on their capacity to withstand particular types of forces, it is crucial to understand the distinction between these two types of stress.
Summary
This article presented compressive stress, explained what it is, and discussed the various formulas needed to find it. To learn more about compressive stress, contact a Xometry representative.
Xometry provides a wide range of manufacturing capabilities, including 3D printing and other value-added services for all of your prototyping and production needs. Visit our website to learn more or to request a free, no-obligation quote.
Disclaimer
The content appearing on this webpage is for informational purposes only. Xometry makes no representation or warranty of any kind, be it expressed or implied, as to the accuracy, completeness, or validity of the information. Any performance parameters, geometric tolerances, specific design features, quality and types of materials, or processes should not be inferred to represent what will be delivered by third-party suppliers or manufacturers through Xometry’s network. Buyers seeking quotes for parts are responsible for defining the specific requirements for those parts. Please refer to our terms and conditions for more information.
.webp)