Mandrel Pipe Benders-Creating the Perfect Curve
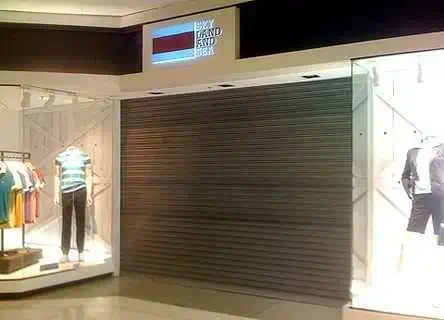
Mandrel pipe benders are an essential tool in the metalworking industry, allowing for the creation of perfect curves in pipes and tubing. These machines utilize a mandrel, or solid steel rod, inserted into the inside of the pipe during the bending process to prevent buckling and maintain the shape and integrity of the pipe. This article explores the various aspects of mandrel pipe benders, including their functionality, applications, and the process of creating the perfect curve.
Mandrel pipe benders are widely used in industries such as automotive, aerospace, construction, and manufacturing, where precise and smooth bending of pipes is required. The ability to create uniform and accurate bends in pipes is crucial for ensuring the structural integrity and performance of various systems and components. By utilizing a mandrel to support the inner wall of the pipe during bending, these machines can produce consistent and high-quality results.
Functionality of Mandrel Pipe Benders
The functionality of mandrel pipe benders is rooted in their ability to control the deformation of the pipe during the bending process. Without a mandrel, pipes are prone to collapsing or wrinkling, especially when bent at tight radii or with thin walls. The mandrel provides internal support, preventing these undesirable outcomes and allowing for the creation of smooth, wrinkle-free bends.
Mandrel pipe benders typically consist of a machine head, clamping system, mandrel extraction system, and bending dies. The pipe is secured in place by the clamping system, and the mandrel is inserted into the pipe to provide internal support. As the machine head exerts force on the pipe, the bending dies shape the pipe around the mandrel, resulting in a precise bend with minimal distortion.
Applications of Mandrel Pipe Benders
The applications of mandrel pipe benders are diverse, spanning across various industries and sectors. In the automotive industry, mandrel-bent exhaust and intake systems are essential for optimizing engine performance and fuel efficiency. These systems often require complex and tightly bent tubing, which can be achieved with the use of mandrel pipe benders.
In the aerospace industry, mandrel pipe benders are utilized in the fabrication of aircraft components, such as hydraulic and pneumatic systems, where the integrity and reliability of the tubing are critical. The construction industry also benefits from mandrel pipe bending technology, using it to create architectural features, handrails, and HVAC systems with intricate and customized bends.
Moreover, mandrel pipe benders play a vital role in the manufacturing of furniture, industrial equipment, and agricultural machinery, where the precise shaping of pipes and tubing is necessary for assembly and functionality.
The Process of Creating the Perfect Curve
The process of creating the perfect curve with a mandrel pipe bender involves several key steps, each contributing to the overall quality and accuracy of the bend.
First, the operator selects the appropriate mandrel and bending dies based on the specifications of the desired curve and the material properties of the pipe. The mandrel must match the inner diameter of the pipe to provide effective support, while the bending dies determine the radius and angle of the bend.
Next, the pipe is loaded into the machine and secured in place using the clamping system. The mandrel is then inserted into the pipe, ensuring that it extends beyond the bending area to prevent distortion or collapse.
As the machine head begins to exert force on the pipe, the mandrel supports the inner wall, allowing the bending dies to gradually shape the pipe into the desired curve. The operator monitors the bending process, adjusting the machine settings as needed to achieve the precise bend without compromising the integrity of the pipe.
Once the bending is complete, the mandrel is extracted from the pipe, leaving behind a smooth and uniform curve. The finished product is inspected for quality and accuracy, ensuring that it meets the required specifications and standards.
Advantages of Mandrel Pipe Bending
Mandrel pipe bending offers several advantages over other bending methods, making it a preferred choice for many applications. One of the primary advantages is the ability to produce tight-radius bends without sacrificing the quality of the pipe. This is particularly valuable in industries where space constraints or design requirements demand compact and intricate tubing configurations.
Additionally, mandrel pipe bending allows for greater control over wall thinning and ovality, preserving the structural integrity of the pipe throughout the bending process. This is especially important for pipes that will be subjected to high-pressure fluids or gases, as any weakening or distortion could compromise the functionality and safety of the system.
Moreover, mandrel pipe bending enables the production of high-quality, aesthetically pleasing bends, making it ideal for applications where the visual appearance of the tubing is a consideration. Whether for architectural features, custom furniture, or decorative elements, mandrel-bent pipes offer a polished and professional look.
Furthermore, the versatility of mandrel pipe benders allows for the bending of various materials, including stainless steel, aluminum, copper, and titanium, expanding the range of applications and industries that can benefit from this technology.
Challenges and Considerations
While mandrel pipe bending offers numerous advantages, there are certain challenges and considerations associated with this process. One of the primary challenges is the selection of the appropriate mandrel and bending dies for a given application. Factors such as material composition, wall thickness, and bend radius must be carefully evaluated to ensure optimal results.
Additionally, the maintenance and upkeep of mandrel pipe bending machines are crucial for consistent performance and longevity. Regular inspection of mandrels, bending dies, and machine components is necessary to identify and address any wear, damage, or misalignment that could affect the quality of bends.
Furthermore, operators must receive comprehensive training and adhere to best practices when using mandrel pipe benders to minimize the risk of errors, accidents, and material waste. Proper understanding of machine settings, material behavior, and bending techniques is essential for achieving precise and reliable results.
Future Developments and Innovations
The field of mandrel pipe bending continues to see advancements and innovations aimed at improving efficiency, precision, and versatility. One area of development is the integration of advanced automation and robotics into pipe bender for sale mandrel pipe bending processes, enabling greater consistency and productivity while reducing manual labor and human error.
Furthermore, advancements in material science and metallurgy are expanding the capabilities of mandrel pipe bending, allowing for the shaping of increasingly exotic and high-strength alloys with enhanced performance characteristics. This opens up new possibilities for applications in industries such as aerospace, defense, and renewable energy, where specialized materials are in demand.
Moreover, the ongoing refinement of machine design and control systems is contributing to the optimization of mandrel pipe bending, enhancing the accuracy of bends, reducing setup times, and minimizing material waste. These developments are driving the adoption of mandrel pipe bending technology in a broader range of industries and applications.
In conclusion, mandrel pipe benders play a pivotal role in the manufacturing and fabrication of curved pipes and tubing across various industries. Their ability to create precise and uniform bends while maintaining the integrity of the pipe makes them indispensable for applications where quality, reliability, and performance are paramount. As technology continues to advance, mandrel pipe bending processes will become even more efficient, versatile, and capable of meeting the evolving demands of modern engineering and design.
https://oaicon.com/