What restricts the processing quality of high-end bearings
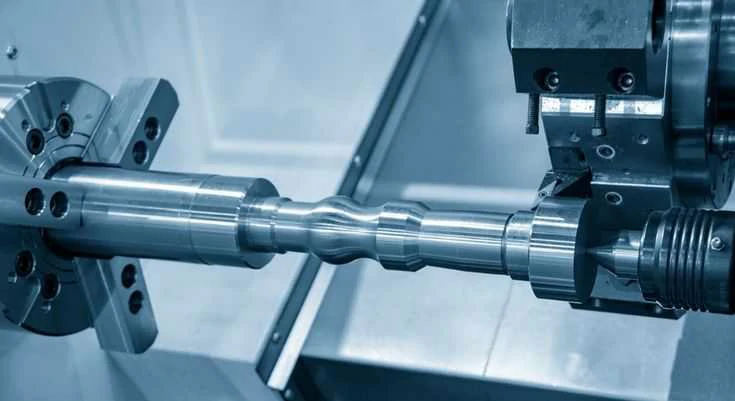
Title: Factors Constraining the Processing Quality of High-End Bearings
Introduction:
High-end bearings play a crucial role in various industries, including automotive, aerospace, and heavy machinery manufacturing. However, achieving superior processing quality in these precision components is challenging due to several factors. This article aims to explore the key constraints that impede the processing quality of high-end bearings.
1. Raw Material Selection:
The quality of raw materials used in manufacturing high-end bearings greatly influences their overall performance. Choosing the right material with excellent hardness, resistance to wear and corrosion, and low friction characteristics is critical. Any compromise in selecting the appropriate raw material can lead to reduced processing quality and compromised product performance.
2. Machining Techniques:
Accurate and precise machining techniques are vital for producing high-quality bearings. The use of advanced machinery and cutting-edge technology, such as computer numerical control (CNC) machines, can significantly improve the processing quality. However, limitations in the machining process, such as tool wear, inadequate lubrication, or suboptimal cutting parameters, can result in dimensional inaccuracies and surface defects, compromising the bearing’s functionality.
3. Heat Treatment:
Heat treatment is a critical step in the manufacturing process of high-end bearings. It involves heating and cooling processes to alter the material’s microstructure and enhance its mechanical properties. Improper heat treatment procedures, such as incorrect temperature control, inadequate quenching, or insufficient tempering, can lead to inconsistent hardness, reduced strength, or residual stress buildup, impacting the processing quality of the bearings.
4. Lubrication and Cooling:
Lubrication and cooling are essential aspects of the machining process for high-end bearings. Sufficient and proper lubrication aids in reducing friction and heat generation during machining, preventing excessive tool wear and surface damage. Inadequate lubrication or cooling can result in increased tool wear, poor surface finish, and thermal distortions, affecting the overall processing quality.
5. Inspection and Quality Control:
A robust inspection and quality control process is crucial to ensure the processing quality of high-end bearings. Utilizing advanced inspection techniques, such as coordinate measuring machines (CMMs), laser scanning, and non-destructive testing methodologies, helps detect any dimensional deviations, surface defects, or material inconsistencies. Neglecting thorough inspection or failing to implement quality control measures can result in the production of substandard bearings.
6. Skilled Workforce:
The expertise and skills of the workforce involved in manufacturing high-end bearings significantly impact the processing quality. Well-trained technicians with a deep understanding of machining processes, material properties, and quality control measures are essential. Insufficient training or lack of skilled personnel can lead to errors in process execution, resulting in compromised processing quality.
Conclusion:
The processing quality of high-end bearings is influenced by multiple factors ranging from raw material selection to the expertise of the workforce. Attention to detail throughout the manufacturing process, including material procurement, machining techniques, heat treatment, lubrication, inspection, and adequate training, is essential to achieve superior processing quality. Addressing these constraints will contribute to the production of high-performance bearings that meet the stringent requirements of diverse industries.
.webp)